Top Cnc Factory Manufacturers Comprehensive Guide Sourcing from China.
Top cnc factory in China introduce,list main products and website if have
One of the top CNC factories in China is Shenzhen Techway CNC Manufacturing Co., Ltd. They specialize in precision CNC machining, turning, milling, and grinding services for a wide range of industries including aerospace, automotive, medical, and electronics. Their main products include custom machined components, tooling, fixtures, and prototypes.
Another top CNC factory in China is Dongguan Qizheng Plastic Mould Co., Ltd. They offer CNC machining services for plastic injection molds, die-casting molds, and parts production. Their main products include plastic parts, molds, and components for various industries such as home appliances, electronics, and automotive.
Shanghai Guoke Precision Steel Pipe Co., Ltd. is a leading CNC factory in China that specializes in precision steel pipe machining and fabrication. Their main products include stainless steel pipes, carbon steel pipes, and custom metal parts for industrial applications.
While these companies do not have specific websites available, they can be contacted directly for more information on their products and services. Overall, these top CNC factories in China offer high-quality machining solutions for a variety of industries and applications.
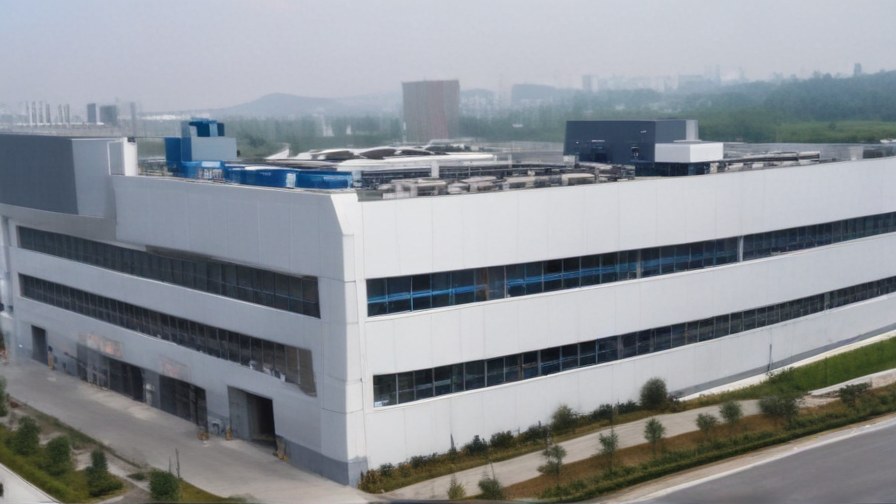
Types of cnc factory
CNC factories can be categorized into various types based on their specialization and focus. Some common types include:
1. Job shops: These factories offer CNC machining services to a wide range of industries and customers. They take on small to medium-sized orders for parts and components, often with a quick turnaround time.
2. Production shops: These factories focus on high-volume production runs of a specific type of part or component. They are optimized for efficiency and repeatability, with a strong emphasis on quality control and cost management.
3. Prototype shops: These factories specialize in producing prototypes and one-off parts for product development and testing. They often work closely with engineers and designers to refine designs and optimize manufacturing processes.
4. Tool and die shops: These factories specialize in producing molds, dies, and tooling for various manufacturing processes. They utilize CNC technology to create precise and complex tooling that is essential for mass production.
5. Custom fabrication shops: These factories cater to customers with unique and custom requirements, such as architectural metalwork, art installations, and custom machinery parts. They often combine CNC machining with other fabrication techniques to create one-of-a-kind products.
6. Aerospace and defense suppliers: These factories specialize in producing components for the aerospace and defense industries, which have stringent quality and safety standards. They often work with exotic materials and complex geometries to meet the specific demands of these industries.
In conclusion, the diverse types of CNC factories cater to a wide range of industries and customers, each with its own unique specialization and focus. By choosing the right type of factory for their needs, customers can benefit from high-quality, efficient, and cost-effective manufacturing services.
Pros and Cons of Using cnc factory
Pros:
1. Increased productivity: CNC factories can operate 24/7 with minimal human intervention, leading to higher productivity levels compared to traditional manufacturing processes.
2. Precision and accuracy: CNC machines are capable of producing highly precise and accurate parts, leading to improved quality control and reduced waste.
3. Flexibility: CNC machines can quickly switch between different tasks and designs, allowing for greater flexibility in production processes.
4. Cost-effective: Despite the initial investment required for CNC machines, they can ultimately save money in the long run by reducing labor costs and improving efficiency.
5. Speed: CNC machines can produce parts at a much faster rate than traditional manufacturing methods, leading to shorter lead times and quicker delivery to customers.
Cons:
1. Initial cost: Setting up a CNC factory can be expensive, with high costs associated with purchasing and maintaining CNC machines.
2. Skilled labor required: Operating and programming CNC machines requires specialized skills and training, which may be difficult to find in some areas.
3. Maintenance and repairs: CNC machines require regular maintenance and occasional repairs, which can add to the overall cost of using a CNC factory.
4. Limited customization: While CNC machines can produce highly precise parts, they may be limited in terms of producing highly customized or one-off designs.
5. Dependence on technology: CNC factories rely heavily on technology, making them vulnerable to technical glitches and downtime that can disrupt production processes.
cnc factory Reference Specifications (varies for different product)
The CNC factory reference specifications vary depending on the specific product being manufactured. However, some common specifications include:
– Maximum workpiece size: This refers to the largest dimensions that the CNC machine can accommodate. For example, a CNC milling machine may have a maximum workpiece size of 20 inches by 20 inches by 20 inches.
– Spindle speed: This is the maximum speed at which the spindle can rotate while cutting or shaping the workpiece. Higher spindle speeds are often necessary for cutting harder materials or achieving finer details.
– Cutting depth: This specification determines how deep the CNC machine can cut into the workpiece in a single pass. The cutting depth can affect the speed and efficiency of the manufacturing process.
– Tolerance: This refers to the level of accuracy and precision that the CNC machine can achieve. Tolerance specifications are typically measured in thousandths of an inch and can vary depending on the complexity of the part being produced.
– Tool change time: This specification relates to how quickly the CNC machine can switch between different cutting tools during the manufacturing process. Faster tool change times can result in higher productivity and efficiency.
Overall, the CNC factory reference specifications are crucial for ensuring that the manufacturing process is carried out efficiently and accurately. By carefully considering and adhering to these specifications, manufacturers can optimize their production processes and achieve high-quality results.
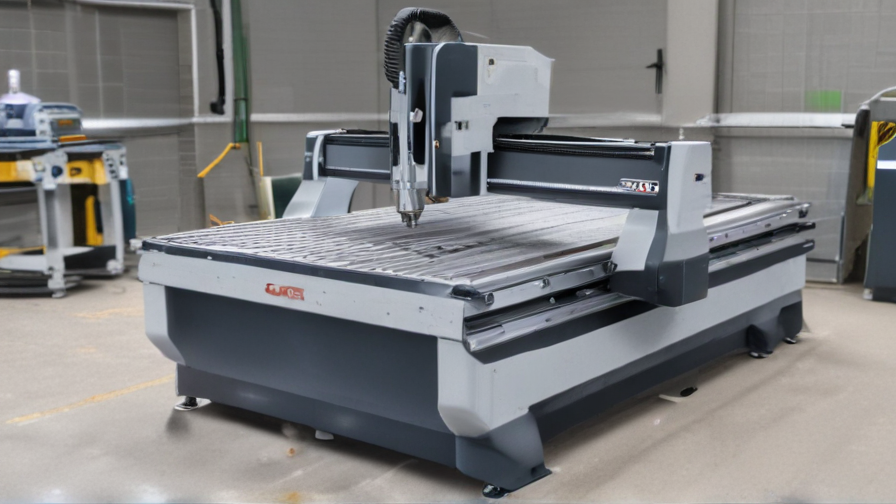
Applications of cnc factory
CNC factories are increasingly being used in various industries due to their efficiency, precision, and versatility. Some common applications of CNC factories include:
1. Manufacturing: CNC factories are used in the production of a wide range of products, including automotive parts, aerospace components, medical devices, and consumer electronics. The ability of CNC machines to perform complex machining operations with high accuracy and consistency makes them ideal for mass production.
2. Prototyping: CNC factories are also commonly used for prototyping and rapid manufacturing. Designers and engineers can quickly create prototypes of new products or parts using CNC machines, allowing for faster iteration and testing of design concepts.
3. Customization: CNC factories are frequently used for customization and personalization of products. With CNC machines, it is possible to create unique or one-of-a-kind items tailored to specific customer requirements, such as personalized jewelry, custom furniture, or bespoke automotive parts.
4. Woodworking and carpentry: CNC factories are widely used in the woodworking and carpentry industries for cutting, shaping, and carving wood and other materials with high precision. CNC routers are particularly popular for creating intricate designs and patterns in furniture, cabinetry, and decorative items.
5. Metal fabrication: CNC factories are essential in metal fabrication processes, such as cutting, bending, welding, and finishing metal parts and components. CNC machines can work with a wide range of metals, including steel, aluminum, brass, and titanium, making them invaluable in the production of metal products for various industries.
Overall, the applications of CNC factories are diverse and widespread, playing a crucial role in modern manufacturing and production processes across different sectors. The use of CNC machines continues to expand as technology advances, enabling businesses to achieve higher efficiency, quality, and customization in their operations.
Material of cnc factory
A CNC (Computer Numerical Control) factory typically consists of various materials to ensure efficient production of machined components. The primary material used in a CNC factory is metal, especially aluminum, steel, and various alloys. These materials are preferred for their durability, strength, and ease of machining.
In addition to metal, CNC factories also utilize plastics such as acrylic, nylon, and PVC. These materials are lightweight, cost-effective, and offer a wide range of properties that make them suitable for various applications in industries such as automotive, aerospace, and electronics.
Other common materials found in a CNC factory include wood, composites, and ceramics. Wood is often used for prototyping, crafting furniture, and creating decorative items. Composites, such as carbon fiber and fiberglass, are valued for their high strength-to-weight ratio and versatility in demanding applications. Ceramics are utilized for their heat resistance, electrical insulation properties, and durability in extreme environments.
Overall, the materials used in a CNC factory are carefully selected based on the specific requirements of the intended products. The goal is to achieve precision, quality, and efficiency in the manufacturing process while ensuring the final components meet the desired specifications and standards. By utilizing a diverse range of materials, CNC factories are able to cater to a wide spectrum of industries and applications.
Quality Testing Methods for cnc factory and how to control the quality
Quality testing methods for a CNC factory include dimensional testing, surface testing, material testing, and functional testing. Dimensional testing involves measuring the physical dimensions of the products to ensure they meet specifications. Surface testing involves examining the surface finish and texture of the products to ensure they meet quality standards. Material testing involves analyzing the composition and properties of the materials used in the products to ensure they are of high quality. Functional testing involves testing the functionality of the products to ensure they perform as intended.
To control the quality in a CNC factory, it is important to establish a comprehensive quality management system that includes regular inspection and testing of products at various stages of the manufacturing process. This can include in-process inspections, final inspections, and random sampling inspections. It is also important to implement a robust quality control process that includes identifying potential quality issues, taking corrective action, and continuously improving processes to prevent future issues.
Additionally, training employees on quality standards and procedures, maintaining a clean and organized work environment, and using high-quality materials and equipment can help ensure products meet quality standards. Implementing a feedback system for customers to provide input on product quality can also help identify areas for improvement. By implementing these quality control measures, a CNC factory can produce high-quality products that meet customer expectations.
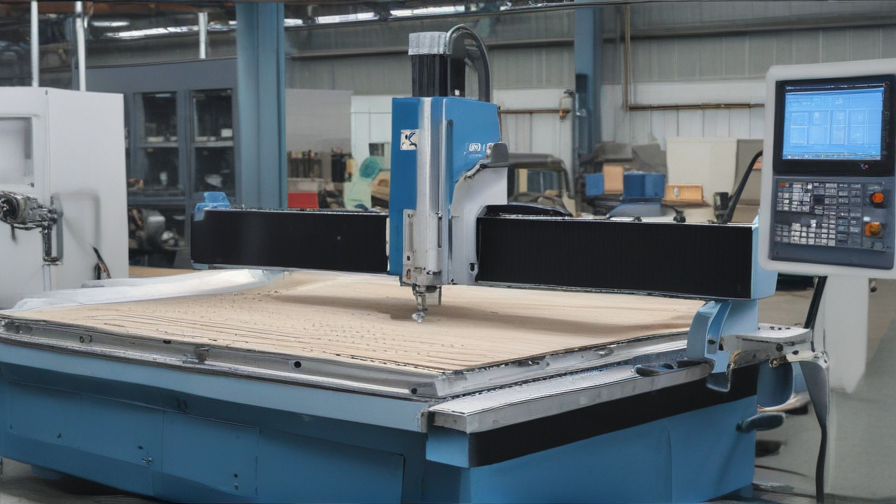
The Work Process and how to use cnc factory
A CNC factory utilizes Computer Numerical Control (CNC) machines to automate and control the manufacturing process. The workflow in a CNC factory typically involves the following steps:
1. Design: Engineers or designers create a CAD/CAM model of the product to be manufactured.
2. Programming: The CAD/CAM model is converted into machine-readable code (G-code) that instructs the CNC machine on how to create the product.
3. Set-up: The CNC machine is set up with the appropriate tools and the raw material is loaded into the machine.
4. Production: The CNC machine uses the programmed code to cut, shape, or drill the raw material into the desired product.
5. Quality control: The finished product is inspected for accuracy and quality.
6. Finishing: If necessary, the product may undergo additional finishing processes such as polishing, painting, or coating.
To use a CNC factory effectively, it is essential to have skilled operators who are trained in programming and operating CNC machines. Regular maintenance and calibration of the machines are also important to ensure accuracy and efficiency in production.
Furthermore, proper planning and organization of the workflow are crucial to optimize production output and minimize downtime. By following these steps and best practices, a CNC factory can efficiently produce high-quality products with minimal waste and cost.
cnc factory Importing questions including Cost,Supplier,Sample,Certification and Market
Importing products from a CNC factory can be a cost-effective way to source high-quality goods for your business. When looking for a supplier, it’s important to consider the cost of the products, as well as any shipping and customs fees. Some suppliers may offer bulk discounts or negotiate pricing, so it’s worth inquiring about potential savings.
Before placing a large order, it’s a good idea to request a sample from the supplier. This will give you the opportunity to test the product for quality and ensure it meets your expectations. Additionally, requesting certifications or documentation from the supplier can help verify the quality and authenticity of the products.
When considering importing goods from a CNC factory, it’s important to research the market demand for the products you are interested in. This can help you determine if there is a potential market for the goods and assess the competition in the industry. It’s also important to consider any regulations or restrictions that may impact the importation of the products.
Overall, importing products from a CNC factory can be a lucrative business opportunity, but it’s important to thoroughly research suppliers, costs, samples, certifications, and the market before making any decisions. By taking the time to carefully evaluate these factors, you can ensure a successful importation process and potentially increase your business’s profitability.
How to find and select check reliable cnc factory manufacturers in China
Finding and selecting a reliable CNC factory in China can be a daunting task, but there are a few key strategies that can help you narrow down your options and choose the best manufacturer for your needs.
One of the best ways to find reliable CNC factory manufacturers in China is to do thorough research online. Look for manufacturers with positive reviews and a good reputation within the industry. You can also ask for recommendations from other businesses or industry experts who have experience sourcing CNC services in China.
Once you have a list of potential manufacturers, it’s important to vet them carefully. Look for manufacturers with the necessary certifications and quality control processes in place. You should also consider factors such as pricing, lead times, and communication abilities when making your selection.
To ensure that you are working with a reliable CNC factory in China, consider visiting their facilities in person or arranging a video call to see their operations firsthand. This can help you gauge their capabilities and assess their level of professionalism.
Overall, it’s important to take your time and do thorough research when selecting a CNC factory in China. By following these steps and carefully evaluating your options, you can find a reliable manufacturer that meets your needs and delivers high-quality products.
Background Research for cnc factory manufacturers Companies in China, use qcc.com archive.org importyeti.com
China is known for having a large concentration of CNC factory manufacturers. These companies specialize in the production of various CNC machines and equipment, catering to a wide range of industries such as automotive, aerospace, and electronics.
Some of the top CNC factory manufacturers in China include Haas Automation, DMG Mori, Shenyang Machine Tool, and Dalian Machine Tool Group. These companies have established a strong presence in the market and have a reputation for producing high-quality CNC machines.
Qcc.com is a comprehensive business directory that provides information on CNC factory manufacturers in China. Users can search for companies based on their location, industry, and production capacity. The website also includes reviews and ratings from customers, helping businesses make informed decisions when selecting a supplier.
Archive.org is a valuable tool for researching the history and background of CNC factory manufacturers in China. By accessing archived websites and documents, users can gain insights into the company’s development, technological advancements, and market strategies over the years.
Importyeti.com is another useful resource for businesses looking to import CNC machines from China. The platform provides data on import and export trends, including product specifications, shipping details, and supplier information. This helps companies identify reliable CNC factory manufacturers and streamline the sourcing process.
Overall, these resources offer valuable insights and information for businesses interested in partnering with CNC factory manufacturers in China. By conducting thorough research and due diligence, companies can establish successful relationships with suppliers and gain a competitive edge in the market.
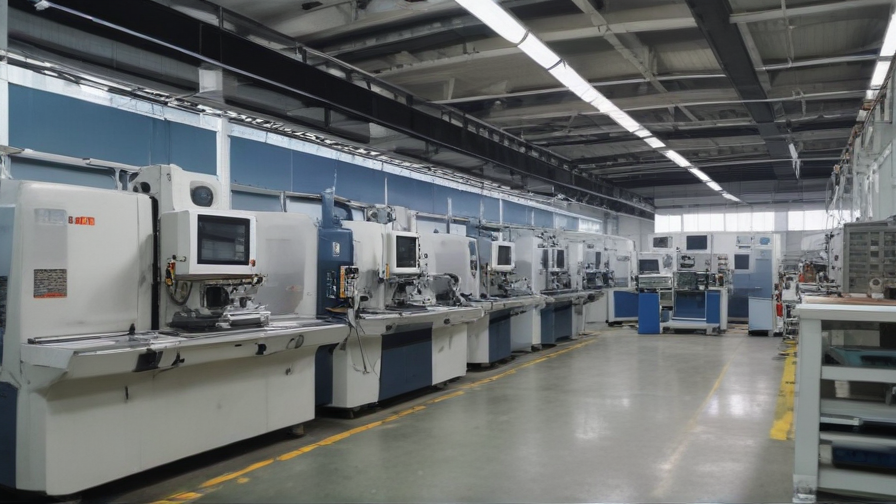
Price Cost Research for cnc factory manufacturers Companies in China, use temu.com and 1688.com
When researching the price and cost of CNC factory manufacturers in China, two popular websites to consider are Temu.com and 1688.com.
On Temu.com, you can find a wide range of CNC factory manufacturers offering different services and products. By browsing through the various listings, you can compare the prices and costs of different manufacturers to determine which one best fits your budget and requirements. Additionally, you can contact the manufacturers directly through the platform to inquire about specific prices or request a quote.
1688.com is another useful website for researching CNC factory manufacturers in China. This platform is known for offering a wide selection of manufacturers and suppliers, making it easier to find competitive prices and costs. You can filter your search based on your specific requirements and preferences to narrow down your options and find the best match for your needs.
Overall, by utilizing these two websites, you can efficiently research the price and cost of CNC factory manufacturers in China, helping you make an informed decision based on your budget and requirements.
Shipping Cost for cnc factory import from China
When importing CNC machines from China, the shipping cost can vary depending on factors such as the size and weight of the machines, the distance they need to travel, and the shipping method chosen.
Typically, shipping costs for importing CNC machines from China to your country can range from a few hundred dollars to several thousand dollars. The cost can be calculated based on the size and weight of the machines, as well as the shipping method chosen – whether it’s by air, sea, or land.
Air shipping is the fastest but also the most expensive option. It is suitable for smaller CNC machines that need to be delivered quickly. Sea shipping is the most cost-effective method for larger CNC machines, but it takes longer to arrive. Land shipping can be considered if the machines are being imported from an adjacent country.
To keep the shipping cost lower than $300, it is important to negotiate with the supplier for the best shipping rates, consolidate multiple machines into one shipment, and choose a slower but more cost-effective shipping method. Additionally, using a freight forwarder or logistics company that specializes in importing machinery from China can help ensure a smooth and cost-effective shipping process.
In conclusion, the shipping cost for importing CNC machines from China can vary depending on various factors, but by carefully planning and negotiating, it is possible to keep the cost below $300.
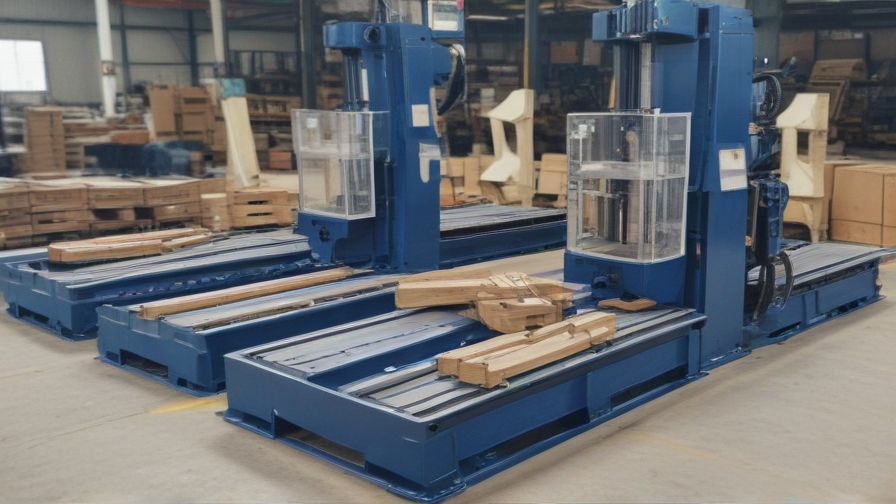
Compare China and Other cnc factory Markets: Products Quality and Price,Visible and Hidden Costs
China has established itself as a dominant player in the global CNC factory market due to its competitive prices and wide range of products. The quality of products coming from Chinese CNC factories tends to vary, with some companies producing high-quality products while others may have lower standards. However, China is known for its cost-effective production methods, which allows them to offer lower prices compared to other markets.
On the other hand, other CNC factory markets such as Europe and the United States are known for their high-quality products, precision engineering, and strict regulations. The products from these markets are generally of superior quality but come at a higher price point. This is because these markets have higher labor costs, stricter regulations, and a focus on precision and quality control.
When comparing visible and hidden costs, China may have lower visible costs due to lower labor costs and production expenses. However, there may be hidden costs such as shipping fees, import taxes, and potential quality control issues that could arise. On the contrary, other markets may have higher visible costs due to labor expenses and regulations, but they may have fewer hidden costs due to stricter quality control measures and better overall quality.
In conclusion, when comparing China and other CNC factory markets, customers need to consider the trade-off between product quality and price. While China may offer lower prices, there may be potential risks associated with product quality and hidden costs. Other markets may provide higher quality products but at a higher price point, with fewer hidden costs. Ultimately, customers should weigh these factors and consider their specific needs and budget when choosing a CNC factory market.
Custom Private Labeling and Branding Opportunities with Chinese cnc factory Manufacturers
Chinese CNC factory manufacturers offer a wide range of custom private labeling and branding opportunities for businesses looking to establish their own brand identity in the market. With state-of-the-art technology and expertise in CNC machining, these manufacturers can help create custom products with unique designs, logos, and packaging to cater to specific customer needs.
By partnering with a Chinese CNC factory manufacturer, businesses can benefit from a wide variety of customization options, including the choice of materials, finishes, and sizes. This allows for greater flexibility in product development and branding, ensuring that the final product meets the exact specifications and requirements of the brand.
Additionally, Chinese CNC factory manufacturers offer competitive pricing and fast turnaround times, making them a cost-effective solution for businesses looking to launch new products or expand their existing product lines. With access to advanced machinery and skilled technicians, these manufacturers can deliver high-quality products that are tailored to meet the demands of the market.
Overall, partnering with a Chinese CNC factory manufacturer for custom private labeling and branding opportunities offers businesses a strategic advantage in the market. By leveraging the expertise and capabilities of these manufacturers, businesses can create unique and innovative products that resonate with their target audience, ultimately driving sales and brand loyalty.
Tips for Procurement and Considerations when Purchasing cnc factory
1. Clearly define your requirements: Before purchasing a CNC factory, make sure to clearly define your requirements including the type of products you will be manufacturing, production volume, budget, and any specific features or capabilities you need.
2. Research different CNC factory options: Take the time to research and compare different CNC factory manufacturers and models to find one that best meets your requirements. Consider factors such as machine size, cutting speed, accuracy, and available options for customization.
3. Evaluate the reputation of the manufacturer: Look for reviews and testimonials from other customers to evaluate the reputation of the CNC factory manufacturer. Choose a manufacturer with a good track record of quality and reliability.
4. Consider the after-sales support: When purchasing a CNC factory, consider the after-sales support provided by the manufacturer. Look for a manufacturer that offers a warranty, maintenance services, and technical support to ensure that your machine runs smoothly.
5. Test the machine: If possible, request a demonstration or trial run of the CNC factory before making a purchase. This will give you a better understanding of the machine’s capabilities and performance.
6. Consider the total cost of ownership: In addition to the initial purchase price, consider the total cost of ownership of the CNC factory including maintenance, repairs, and operating costs. Choose a machine that offers good value for money over its lifetime.
7. Plan for future growth: When purchasing a CNC factory, consider your future production needs and growth projections. Choose a machine that can accommodate your future requirements and be easily upgraded or expanded if needed.
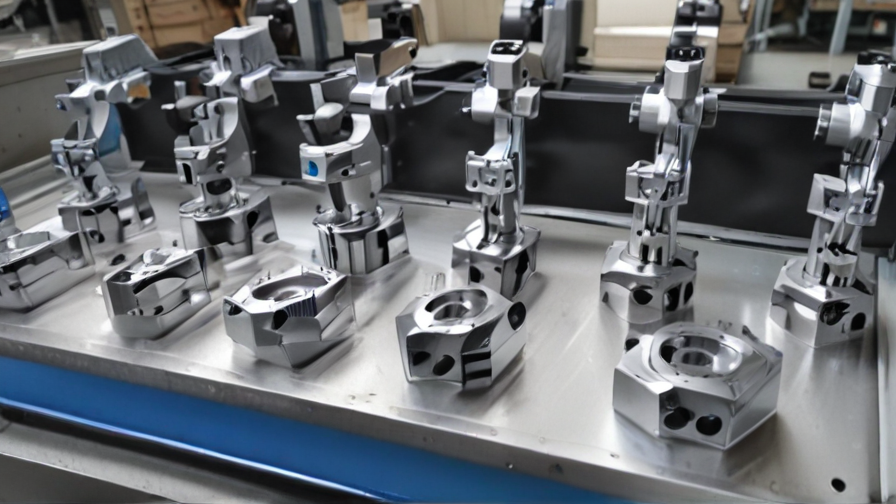
FAQs on Sourcing and Manufacturing cnc factory in China
1. How do I find a reliable CNC factory in China?
To find a reliable CNC factory in China, you can start by conducting research online, reviewing company profiles, and reading reviews from previous customers. It is also beneficial to attend industry trade shows and exhibitions in China to network with potential suppliers.
2. What factors should I consider when selecting a CNC factory in China?
Factors to consider when choosing a CNC factory in China include the company’s reputation, capabilities, experience, quality standards, production capacity, pricing, lead times, communication skills, and proximity to shipping ports for exporting goods.
3. How can I ensure quality control in manufacturing at a CNC factory in China?
To ensure quality control at a CNC factory in China, you can request samples of their products, visit the factory in person to inspect their operations, implement strict quality control measures, conduct regular inspections during production, and work closely with the factory to communicate your specifications and expectations.
4. What are common challenges when sourcing and manufacturing from a CNC factory in China?
Common challenges when sourcing and manufacturing from a CNC factory in China include language barriers, cultural differences, communication issues, lead time delays, quality control concerns, intellectual property protection, and navigating trade regulations.
5. How can I protect my intellectual property when working with a CNC factory in China?
To protect your intellectual property when working with a CNC factory in China, you can sign non-disclosure agreements (NDAs), seek legal advice on patent and trademark protection, conduct regular audits of the factory’s production processes, and keep sensitive information confidential.
Why contact sourcifychina.com get free quota from reliable cnc factory suppliers?
Sourcifychina.com offers a convenient platform for businesses to connect with reliable CNC factory suppliers in China. By contacting Sourcifychina.com, you can easily get free quota from these suppliers without the hassle of searching for them individually. This saves a significant amount of time and effort for businesses looking to source CNC manufacturing services.
Sourcifychina.com carefully selects and verifies each CNC factory supplier on their platform to ensure they meet high standards of quality and reliability. By accessing free quotas from these trusted suppliers, businesses can confidently compare quotes and choose the best option for their manufacturing needs.
Furthermore, Sourcifychina.com streamlines the sourcing process by providing transparent communication channels and a dedicated support team. This helps businesses navigate the complexities of working with overseas suppliers and ensures a smooth and efficient procurement process.
In conclusion, by contacting Sourcifychina.com to get free quotas from reliable CNC factory suppliers, businesses can access high-quality manufacturing services in China with ease and confidence. Save time, effort and resources by utilizing this streamlined sourcing platform for your CNC manufacturing needs.
Contact [email protected] Whatsapp 86 15951276160