Top Punching Parts Manufacturers Comprehensive Guide Sourcing from China.
Top punching parts in China introduce,list main products and website if have
One of the top manufacturers of punching parts in China is Dongguan Changyuan Industry Co., Ltd. They specialize in producing a wide range of punching parts, including precision metal stamping parts, deep drawn parts, and progressive die stamping parts. Their products are used in various industries such as automotive, electronics, and hardware.
Another reputable manufacturer is Shenzhen Mingxing Precision Hardware Co., Ltd, which produces punching parts like metal brackets, terminals, and connectors. They have a strong focus on quality control and customer satisfaction.
One more notable manufacturer is Qingdao Tianhua Yihe Foundry Factory, known for their punching parts such as flanges, brackets, and fittings. They offer customized solutions and have a strong reputation for on-time delivery.
For more information on these manufacturers and their products, you can visit their respective websites:
1. Dongguan Changyuan Industry Co., Ltd – Website: www.dgcyindustry.com
2. Shenzhen Mingxing Precision Hardware Co., Ltd – Website: www.szmxdz.com
3. Qingdao Tianhua Yihe Foundry Factory – Website: www.qdthyh.com
These manufacturers are known for their high-quality punching parts, competitive pricing, and commitment to customer satisfaction. Whether you are looking for standard punching parts or customized solutions, these companies can meet your needs.
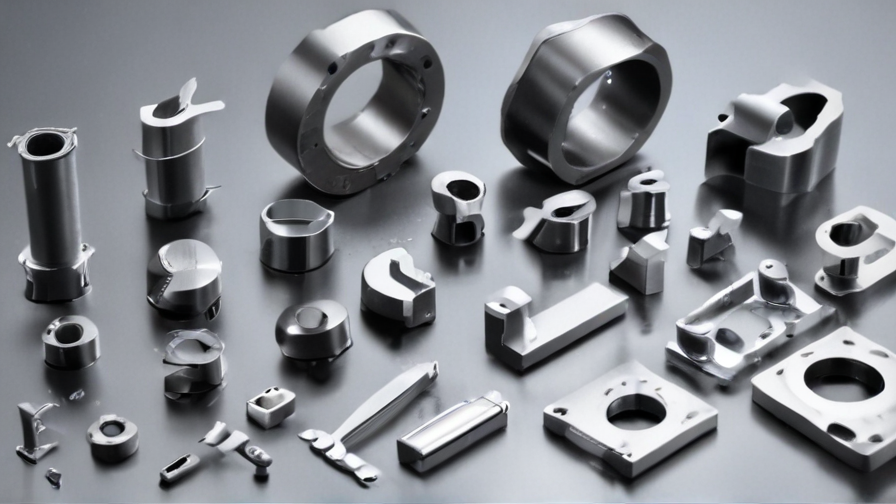
Types of punching parts
There are a variety of punching parts used in various industries and applications. Some common types include:
1. Punches: These are tools used to create holes or shapes in materials. They can come in various shapes and sizes, such as round, square, or oval punches.
2. Dies: These are tools used in conjunction with punches to cut or form materials. Dies are typically made from hardened steel and can have various shapes and sizes to create different designs.
3. Blanking punches: These are used to cut out specific shapes from a larger piece of material. Blanking punches are commonly used in the automotive industry to create parts such as metal panels or brackets.
4. Embossing punches: These tools are used to create raised or sunken designs on a material’s surface. Embossing punches are often used in decorative applications, such as creating logos or patterns on leather or paper products.
5. Notching punches: These tools are used to create notches or grooves in materials. Notching punches are commonly used in metalworking to create precise cuts in sheet metal or tubing.
6. Piercing punches: These tools are used to create holes in materials without removing any material. Piercing punches are commonly used in the production of textiles, leather goods, and paper products.
Overall, punching parts play a crucial role in manufacturing processes across a variety of industries. By using the right type of punching part for each application, manufacturers can efficiently produce high-quality parts and products.
Pros and Cons of Using punching parts
Punching parts are commonly used in various industries such as automotive, electronics, and construction for cutting or shaping materials like metal, plastic, and paper. There are several advantages and disadvantages to using punching parts in manufacturing processes.
Pros:
1. Precision and accuracy: Punching parts provide a highly precise and accurate cutting or shaping of materials, ensuring consistent and high-quality products.
2. Cost-effective: Punching parts are relatively cost-effective compared to other cutting methods, making them a cost-efficient option for manufacturers.
3. Speed: Punching parts can operate at high speeds, leading to increased productivity and shorter production times.
4. Versatility: Punching parts can be used for a wide range of materials and shapes, making them versatile and adaptable for various manufacturing needs.
5. Low maintenance: Punching parts are generally easy to maintain and require minimal upkeep, reducing downtime and maintenance costs.
Cons:
1. Limited flexibility: Punching parts may have limitations in terms of the complexity of shapes and sizes that can be achieved, especially compared to other cutting methods like laser cutting.
2. Tool wear: The punching tools used in punching parts can wear out over time, leading to additional costs for replacement and maintenance.
3. Material distortion: Punching parts can sometimes lead to material distortion or deformation, particularly in thin or soft materials.
4. Noise and vibrations: The high-speed operation of punching parts can generate noise and vibrations, potentially causing issues with workplace safety and comfort.
5. Setup time: Changing punching tools and adjusting settings for different materials or shapes can require additional setup time, which may impact production efficiency.
In conclusion, punching parts offer various benefits such as precision, cost-effectiveness, and speed, but they also have limitations in terms of flexibility, tool wear, material distortion, noise, and setup time. Careful consideration of these pros and cons is necessary when deciding whether to use punching parts in manufacturing processes.
punching parts Reference Specifications (varies for different product)
Punching parts are crucial components in various industries such as manufacturing, automotive, and construction. These parts are typically made from materials such as steel, aluminum, or brass and are used to create holes or indentations in other materials. The specifications for punching parts vary depending on the specific product they are intended for.
Some common reference specifications for punching parts include the size of the hole or indentation, the thickness and type of material being punched, the maximum force and speed required for punching, and the overall dimensions and tolerances of the part. These specifications are important to ensure that the punching part functions properly and meets the requirements of the final product.
In addition to these basic specifications, punching parts may also have specific requirements for coatings or treatments to improve durability, corrosion resistance, or appearance. For example, some punching parts may require a coating of zinc or nickel to protect against rust, or a special heat treatment to increase hardness and wear resistance.
Manufacturers of punching parts use advanced technologies such as CNC machining and laser cutting to produce high-precision parts that meet the exact specifications of their customers. These parts are typically produced in large quantities and may be customized to suit specific applications. By adhering to the reference specifications and using the latest manufacturing methods, punching parts manufacturers can produce high-quality parts that meet the demanding requirements of industries around the world.
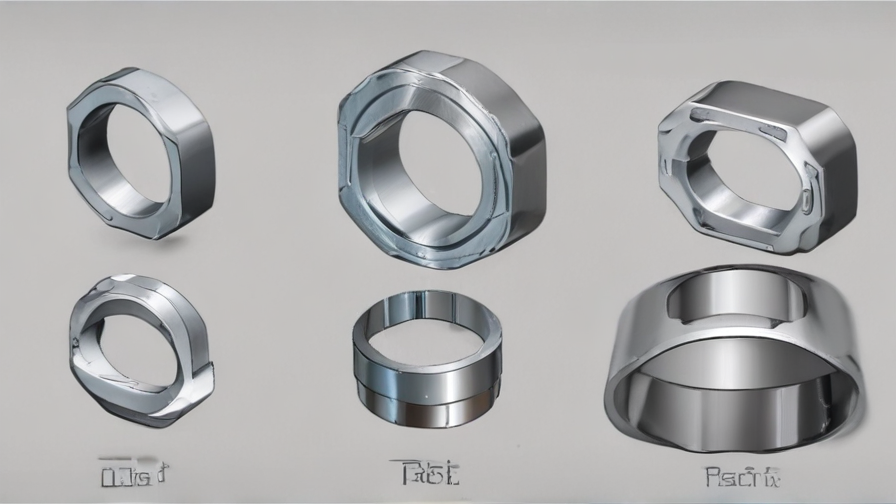
Applications of punching parts
Punching parts are commonly used in various industries for a wide range of applications. One of the most common uses of punching parts is in the automotive industry, where they are used to create precise holes, slots, and shapes in sheet metal for components such as brackets, brackets, and frames. These punched parts help to streamline production processes, reduce costs, and improve overall product quality.
In the electronics industry, punching parts are utilized for creating intricate patterns and designs in sheet metal for components such as computer cases, enclosures, and panels. The precise punching capabilities of these parts allow for the creation of complex shapes and patterns that meet the specific requirements of electronic devices.
Punching parts are also used in the construction industry for creating holes, notches, and slots in various materials, including steel, aluminum, and plastics. These punched parts are essential for connecting elements, securing components, and enhancing the overall functionality of structures.
In the consumer goods industry, punching parts are used for manufacturing a wide range of products, including furniture, appliances, and household items. These parts help to enhance the aesthetic appeal, functionality, and durability of these products, making them more attractive and user-friendly for consumers.
Overall, punching parts play a crucial role in various industries by providing a cost-effective and efficient solution for creating precise holes, shapes, and patterns in a wide range of materials. Their versatility, accuracy, and reliability make them a preferred choice for manufacturers looking to streamline production processes and improve product quality.
Material of punching parts
Punching parts can be made from a variety of materials depending on the specific application and requirements. Some common materials used for punching parts include:
1. Steel: Steel is a commonly used material for punching parts due to its strength, durability, and affordability. It can be hardened and tempered to increase its wear resistance, making it suitable for high-impact applications.
2. Aluminum: Aluminum is another popular material for punching parts due to its lightweight nature and corrosion resistance. It is commonly used in industries such as aerospace and automotive for its strength-to-weight ratio.
3. Brass: Brass is a softer metal that is often used for punching parts that require good electrical conductivity or a decorative finish. It is also corrosion resistant and has excellent machinability.
4. Copper: Copper is another material that is often used for punching parts that require good electrical conductivity. It is also corrosion resistant and has excellent thermal conductivity, making it suitable for heat transfer applications.
5. Plastic: Some punching parts may be made from plastic materials such as nylon, polycarbonate, or PVC. These materials are lightweight, corrosion resistant, and offer good impact resistance. They are commonly used in industries such as electronics and consumer goods.
When selecting a material for punching parts, it is important to consider factors such as the required strength, wear resistance, corrosion resistance, and cost. It is also important to work with a reputable manufacturer who can recommend the most suitable material for your specific application.
Quality Testing Methods for punching parts and how to control the quality
There are a few key quality testing methods that can be used for punching parts to ensure their quality and performance are up to standard.
1. Visual inspection: Conducting a visual inspection of the punched parts can help identify any defects such as cracks, burrs, or uneven edges. This can be done using a magnifying glass or microscope to examine the details of the part.
2. Dimensional inspection: Measuring the dimensions of the punched parts using calipers, micrometers, or coordinate measuring machines (CMM) can help ensure they are within the specified tolerances. This can help identify any variations in size that may affect the part’s functionality.
3. Tensile testing: Tensile testing can be used to determine the strength and ductility of the punched parts. This involves pulling the part to a point of failure and measuring the amount of force required. This can help assess the part’s overall mechanical properties.
To control the quality of punched parts, it is important to establish clear quality standards and procedures for testing. Regularly inspecting and testing the parts throughout the production process can help identify any issues early on and prevent defects from reaching the customer. Additionally, providing proper training to operators and ensuring equipment is properly maintained can help maintain consistent quality in the punching process. Regular audits and reviews of the quality control process can also help identify any areas for improvement and ensure that quality standards are being met. By implementing these quality testing methods and controls, manufacturers can ensure that their punched parts meet the desired quality standards and perform as expected.
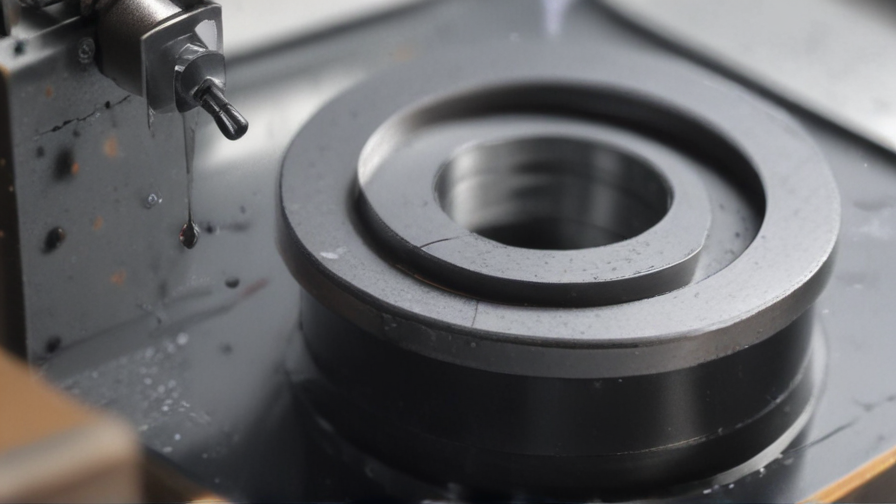
The Work Process and how to use punching parts
The work process of using punching parts involves several key steps to ensure accuracy and efficiency.
First, the punching parts should be selected based on the specific requirements of the project. It is important to carefully review the design specifications and select the appropriate punching parts that match the required dimensions and features.
Next, the punching parts should be securely installed onto the punching machine. This typically involves attaching the parts to the machine using clamps or other securing mechanisms to ensure stability during the punching process.
Once the punching parts are properly installed, the punching operation can begin. The operator should carefully position the material to be punched under the punching parts, ensuring alignment with the desired punching locations.
The punching machine should be carefully calibrated to ensure the correct force and speed are applied during the punching process. This will help prevent damage to the punching parts and ensure a clean and accurate punch every time.
After the punching operation is complete, the punched material can be removed from the machine and inspected for any defects or inconsistencies. Any necessary adjustments can be made to the punching parts or machine settings to improve the quality of future punches.
Overall, the work process of using punching parts involves careful selection, installation, operation, and inspection to ensure accurate and efficient punching results. By following these steps, operators can maximize the effectiveness of punching parts and produce high-quality punched materials for various applications.
punching parts Importing questions including Cost,Supplier,Sample,Certification and Market
When importing punching parts, there are several key questions to consider.
Cost is a crucial factor when importing punching parts as it directly impacts your bottom line. It is important to consider not just the unit cost of the parts, but also shipping costs, duties, and any other associated fees. Comparing costs from different suppliers will help you find the most cost-effective option.
Supplier selection is another important consideration when importing punching parts. You’ll want to find a reliable supplier with a good reputation for quality and timely delivery. Conducting thorough research, reading reviews, and requesting references can help you choose the right supplier for your needs.
Sampling is often recommended before placing a bulk order of punching parts. Requesting samples allows you to assess the quality of the parts, check for any defects, and ensure they meet your specifications. This can help you avoid potential issues once you place a larger order.
Certification is also an important consideration when importing punching parts, especially if they are intended for use in regulated industries. Ensuring that the parts meet relevant industry standards and have the necessary certifications can help you avoid compliance issues.
Lastly, consider the market for punching parts in the country where you plan to import them. Understanding demand, competition, and market trends can help you make informed decisions about your import strategy.
By carefully considering these factors – cost, supplier, samples, certification, and market – you can make a successful import of punching parts.
How to find and select check reliable punching parts manufacturers in China
To find and select reliable punching parts manufacturers in China, first conduct thorough research online through platforms such as Alibaba, Made-in-China, or Global Sources. Look for manufacturers with high ratings, positive reviews, and a significant number of years in business.
Next, contact potential manufacturers to request samples of their products for quality testing. Evaluate their response time, communication skills, and willingness to provide information. Ensure they have experience in producing punching parts and can meet your specific requirements.
Additionally, ask for references from other clients to verify the manufacturer’s reputation and reliability. Check if they have certifications such as ISO 9001 to ensure they meet international quality standards.
Consider visiting the manufacturer’s facilities in China to assess their production capabilities, quality control measures, and overall professionalism.
Finally, negotiate pricing, payment terms, and production lead times to ensure they align with your budget and timeline. Choose a manufacturer that offers competitive rates without compromising on product quality.
By following these steps, you can find and select a reliable punching parts manufacturer in China that meets your needs and specifications.
Background Research for punching parts manufacturers Companies in China, use qcc.com archive.org importyeti.com
When looking for punching parts manufacturers in China, QCC.com is a useful resource as it provides information on various companies and their products. Archive.org can also be helpful for background research as it archives old versions of websites, allowing you to see a company’s past performance and reputation. Importyeti.com is another valuable tool for finding manufacturers in China, as it offers data on companies that import and export goods, giving you an idea of their reach and experience in the industry.
By utilizing these resources, you can gather information on a company’s history, product offerings, customer reviews, pricing, and more. This will help you make an informed decision when choosing a punching parts manufacturer in China, ensuring that you partner with a reliable and reputable company that can meet your specific requirements and quality standards.
Overall, conducting background research on punching parts manufacturers in China through QCC.com, Archive.org, and Importyeti.com can help you find a reputable and reliable supplier for your punching parts needs, ensuring a successful partnership and high-quality products.
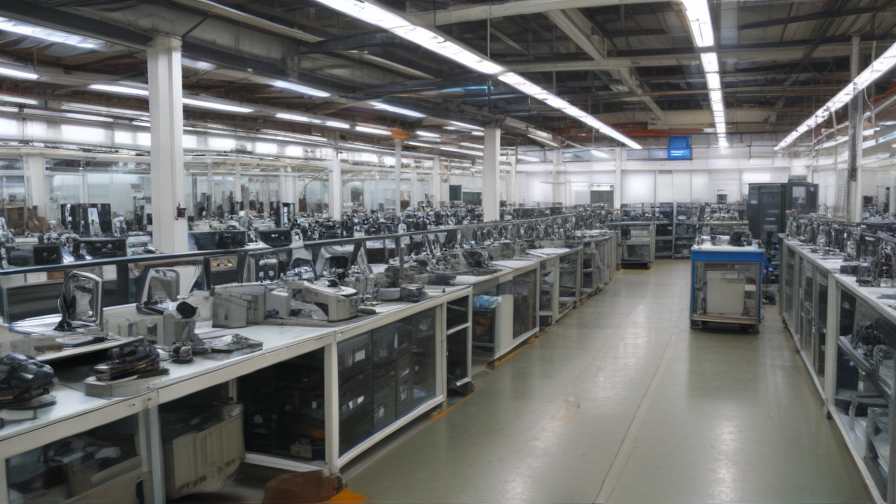
Price Cost Research for punching parts manufacturers Companies in China, use temu.com and 1688.com
When researching punching parts manufacturers in China, two popular platforms to use are temu.com and 1688.com. These websites allow you to easily search for manufacturers and suppliers, as well as compare prices and reviews.
To find pricing information, start by searching for punching parts manufacturers on both platforms. Take note of the different options available and the prices listed for their products. You can also reach out to the manufacturers directly through the platform to inquire about pricing for specific quantities or customization options.
On temu.com, you can use the search bar to find punching parts manufacturers and filter the results based on factors such as price range, location, and capabilities. You can also view detailed product listings and reviews from other buyers to help inform your decision.
Similarly, 1688.com offers a wide selection of punching parts manufacturers to choose from. You can browse categories, read company profiles, and request quotes directly through the platform. Make sure to compare prices from multiple suppliers to ensure you are getting a competitive rate.
In conclusion, using temu.com and 1688.com for price cost research on punching parts manufacturers in China can help you find the best options for your needs while staying within budget. By utilizing these platforms, you can access a wide range of suppliers and compare prices to make an informed decision.
Shipping Cost for punching parts import from China
When importing punching parts from China, you will need to consider the shipping costs involved in getting the goods to your location. The shipping cost for punching parts imported from China can vary depending on a few key factors.
Firstly, the weight and dimensions of the punching parts will play a significant role in determining the shipping cost. Heavier and bulkier items will generally incur higher shipping fees due to the increased fuel and handling required to transport them.
Secondly, the shipping method chosen will also affect the cost. Air freight is typically more expensive than sea freight, but it is also faster and more reliable. If you need the punching parts urgently, air freight may be the best option despite the higher cost.
Additionally, the distance between China and your location will impact the shipping cost. Longer distances will naturally result in higher shipping fees, so it’s important to factor this into your budgeting when importing punching parts from China.
Lastly, customs duties and taxes may also need to be considered when calculating the total cost of importing punching parts from China. These additional fees can vary depending on the country of importation and the type of goods being imported.
To ensure that you do not exceed your budget of 300 words, it is important to research and compare different shipping options, negotiate with suppliers for competitive rates, and factor in all potential costs associated with importing punching parts from China. By carefully planning and budgeting for shipping costs, you can mitigate any unexpected expenses and ensure a smooth and cost-effective importation process.

Compare China and Other punching parts Markets: Products Quality and Price,Visible and Hidden Costs
China has been known as a hub for manufacturing punching parts, offering a wide range of products at competitive prices. The quality of these products can vary significantly, with some Chinese manufacturers producing high-quality parts that meet global standards, while others may offer lower-quality products.
In comparison to other punching parts markets, China generally offers lower prices due to its lower labor costs and economies of scale. However, this lower price point may come with hidden costs such as longer lead times, communication barriers, and potential quality issues. Other markets may offer higher-priced punching parts that come with a guarantee of better quality and reliability.
Visible costs, such as the upfront price of the punching parts, may be more competitive in China, but hidden costs such as shipping, tariffs, and quality control inspections can add up and impact the overall cost of doing business in China. Other markets may have higher upfront costs but may offer a more transparent pricing structure and lower hidden costs.
Overall, while China offers competitive prices and a wide range of punching parts, other markets may offer higher quality products with fewer hidden costs. It is essential for businesses to carefully evaluate their options and consider factors such as product quality, price, and hidden costs when sourcing punching parts from different markets.
Custom Private Labeling and Branding Opportunities with Chinese punching parts Manufacturers
Are you looking to expand your product line with high-quality punching parts from China? Look no further than our Chinese manufacturers who offer custom private labeling and branding opportunities.
Our manufacturers specialize in producing precision punching parts that meet the highest industry standards. With state-of-the-art facilities and a team of experienced engineers, they can customize punching parts to meet your specific requirements.
When you choose to work with our Chinese manufacturers, you can take advantage of our private labeling and branding services. We can help you create custom packaging, labels, and promotional materials that reflect your brand identity. This allows you to offer unique punching parts that stand out in the market and showcase your brand to customers.
Whether you are looking to add punching parts to your existing product line or launch a new product, our Chinese manufacturers can help you every step of the way. From design and prototyping to production and packaging, we can ensure that your punching parts meet your exact specifications and exceed your expectations.
Partner with our Chinese manufacturers today to unlock new possibilities for your business and take advantage of our custom private labeling and branding opportunities. Contact us now to learn more about how we can help you grow your brand with high-quality punching parts from China.
Tips for Procurement and Considerations when Purchasing punching parts
1. Specify your requirements: Clearly define the specifications and requirements for the punching parts you need, including material, dimensions, tolerances, and surface finish. This will help suppliers understand your needs and provide accurate quotes.
2. Research potential suppliers: Look for reputable suppliers with experience in producing punching parts. Check their reputation, capabilities, and quality control processes to ensure they can meet your requirements.
3. Get multiple quotes: Obtain quotes from several suppliers to compare prices, lead times, and quality. This will give you a better understanding of the market and help you make an informed decision.
4. Consider quality over price: While price is important, prioritize quality when selecting a supplier. Low-quality punching parts can lead to production issues and costly rework in the long run.
5. Request samples: Ask for samples of the punching parts before making a large order. This will allow you to inspect the quality and ensure they meet your specifications before committing to a larger purchase.
6. Consider production capacity: Make sure the supplier has the capacity to fulfill your order on time. Consider factors like production lead times, order volume, and any potential bottlenecks in their manufacturing process.
7. Evaluate communication and customer service: Choose a supplier that is responsive, transparent, and willing to work with you to meet your needs. Good communication is essential for a successful procurement process.
8. Consider sustainability and ethical practices: In addition to quality and price, consider the supplier’s sustainability practices, ethical standards, and commitment to social responsibility when selecting a supplier for punching parts.
By following these tips and considerations, you can ensure a smooth and successful procurement process for purchasing punching parts for your manufacturing needs.
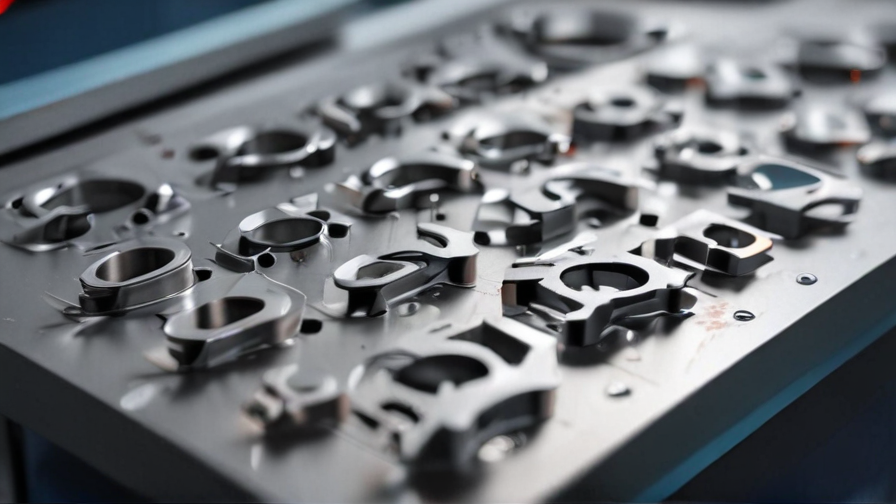
FAQs on Sourcing and Manufacturing punching parts in China
Q: Why should I consider sourcing and manufacturing punching parts in China?
A: China has a well-developed manufacturing industry with a wide range of capabilities, cost-effective labor, and access to a large pool of skilled workers. It is also home to numerous suppliers and manufacturers specializing in punching parts, providing a diverse range of options for sourcing these components.
Q: What factors should I consider when sourcing punching parts in China?
A: When sourcing punching parts in China, it is important to consider the supplier’s experience and reputation, production capabilities, quality control measures, and their ability to meet your specific requirements and timelines. Communication and cultural differences may also play a role in ensuring a successful partnership.
Q: How can I ensure quality control when manufacturing punching parts in China?
A: To ensure quality control when manufacturing punching parts in China, it is important to work with reputable suppliers who have established quality management systems in place. Regular inspections, audits, and clear communication on quality standards and specifications are key to maintaining the desired level of quality.
Q: How can I manage logistics and shipping when sourcing punching parts from China?
A: Managing logistics and shipping when sourcing punching parts from China involves coordinating with suppliers, freight forwarders, and customs agents to ensure timely delivery of parts. Clear communication, proper documentation, and contingency planning can help mitigate potential delays and ensure a smooth shipping process.
Why contact sourcifychina.com get free quota from reliable punching parts suppliers?
Sourcifychina.com offers a convenient platform for businesses to connect with reliable suppliers of punching parts in China. By contacting Sourcifychina.com, companies can easily request a free quota from multiple suppliers to ensure they are getting the best deal possible. This saves time and effort that would normally be spent researching and negotiating with suppliers individually.
Additionally, working with reputable suppliers through Sourcifychina.com ensures that businesses can access high-quality punching parts that meet their specific requirements. The platform only partners with trusted suppliers who have a proven track record of delivering top-notch products and services.
By leveraging the resources and network of Sourcifychina.com, businesses can streamline their sourcing process and maximize cost savings. The platform also provides support and guidance throughout the entire procurement process, making it easier for companies to navigate the complexities of sourcing from overseas suppliers.
Overall, contacting Sourcifychina.com to get a free quota from reliable punching parts suppliers is a smart business decision that can help companies save time, money, and hassle while securing high-quality products for their manufacturing needs.
Contact [email protected] Whatsapp 86 15951276160